PRODUCTION OF HIGH-PRECISION DETAILS…
1. Precision Mechanics
Production of high-precision details using cutting technology for the medical, aviation, defense, mechanical, etc., industries. We offer comprehensive customer service from the project to the production of finished elements on highly specialized CNC machines of the Swiss company Tornos.
Our lathes ensure the maintenance of strictly defined tolerances and repeatability at the highest level. We specialize in the processing of titanium alloys and stainless steel.
SUPPORT
Within the framework of cooperation, we offer the following services:
- design consultancy
- prototype production according to client’s indications
- production of finished elements
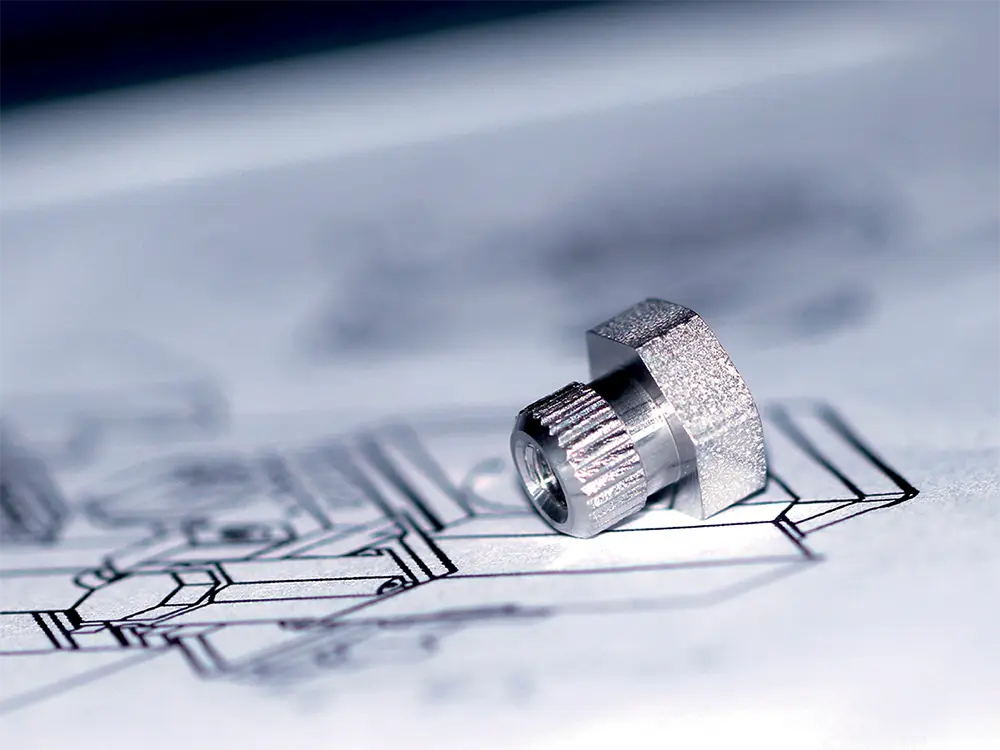
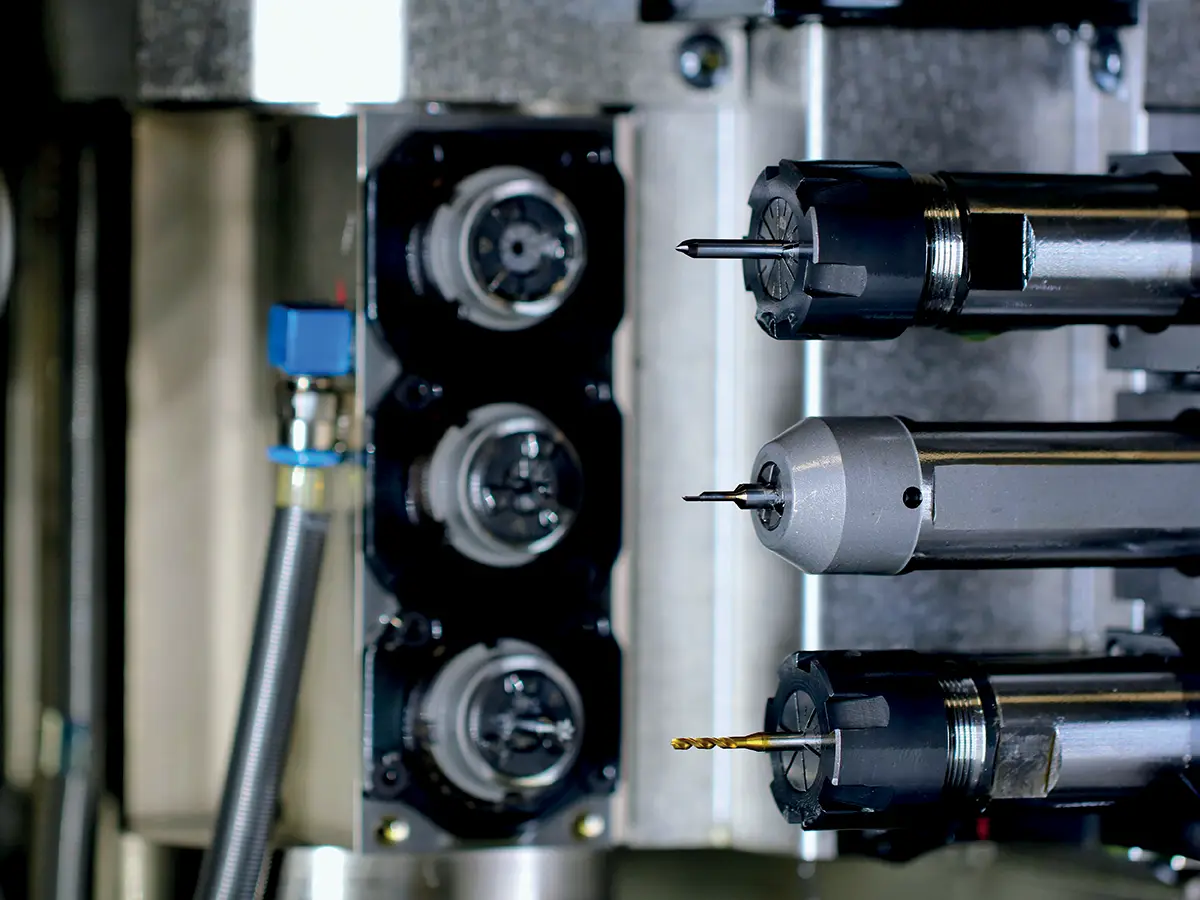
EASY PRODUCT IDENTIFICATION…
2. Laser Marking
Laser marking using a contactless printing method significantly facilitates product identification, allows for its personalization, and makes it recognizable.
It finds application in many industries. We can successfully perform services for the mechanical, medical, defense, aviation, cosmetic, electromechanical, advertising, and many other industries.
SCOPE OF SERVICES
Within the framework of cooperation, we perform:
- product coding
- date application
- alphanumeric and marketing marking
- identifiers
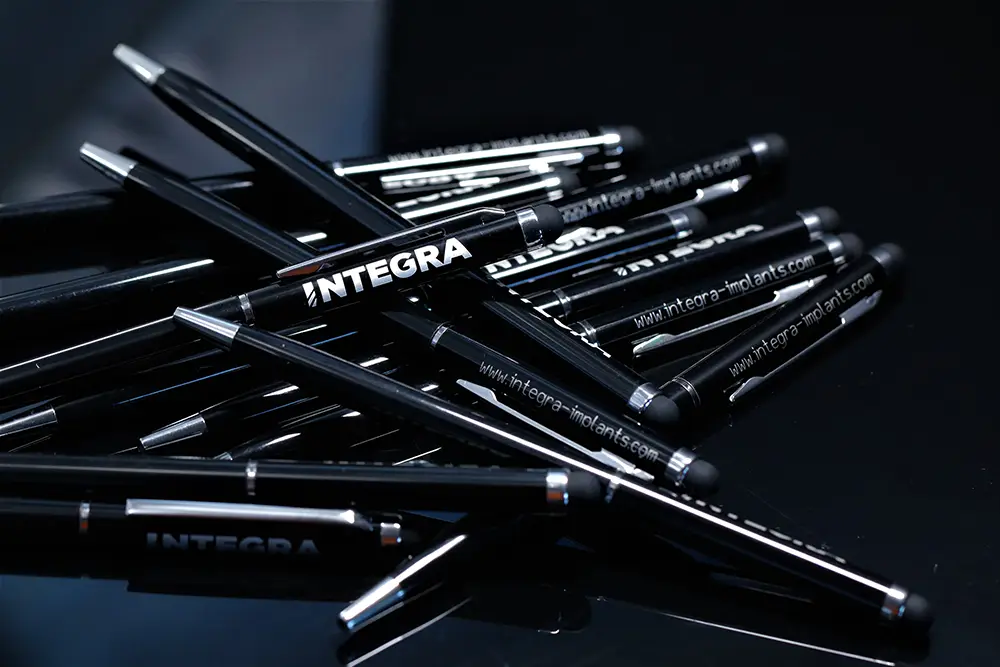
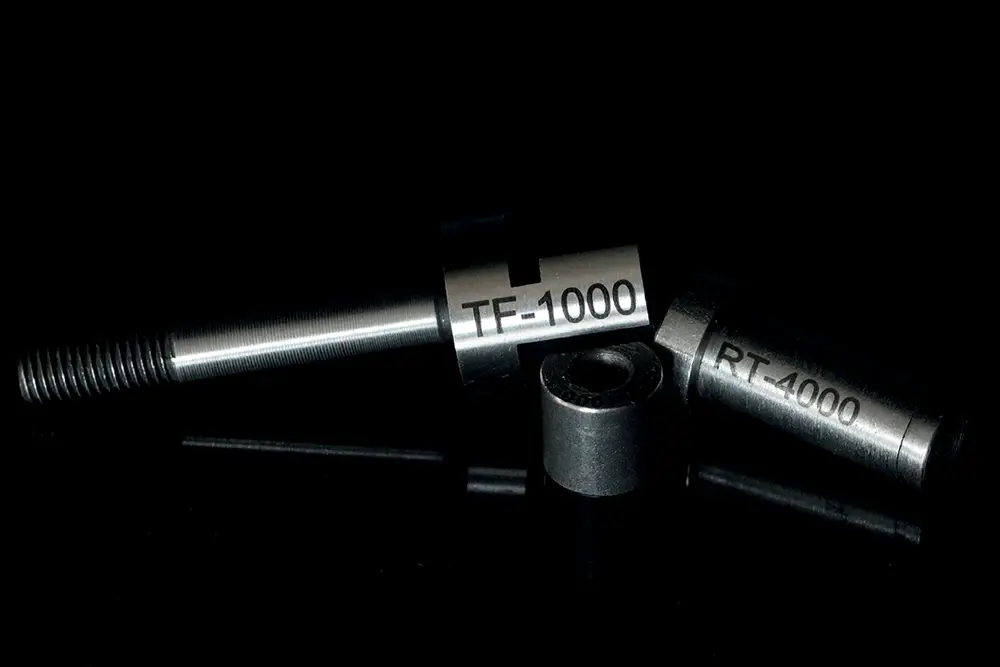
Obróbka elementów…
3. Titanium Oxide Anodizing
Processing of elements during the electrochemical process, during which a layer of titanium oxide is formed on the surface of the metal.
Titanium and its alloys are widely used in many branches of technology, thanks to their physicochemical properties. One of the methods to improve the desired features of titanium is to subject it to electrolytic oxidation, i.e., anodizing.
BIOCOMPATIBILITY
The titanium oxidation process we conduct in phosphoric acid solution is characterized by the ability to increase biocompatibility, which is caused by the interaction of the formed oxide layer with the components of physiological fluid. This consequently leads to the formation of hydroxyapatite and bone tissue growth on the anodized surface.
POSSIBILITIES
An additional effect we achieve in the anodizing process of titanium is the reduction of the release of alloy elements.
The anodizing process also allows for the creation of a colored coating on the surface of the oxidized element.
QUALITY
Titanium details subjected to the process of electrochemical oxidation are cleaned using high-performance ultrasonic cleaners from the Swiss manufacturer KKS Ultraschall AG.
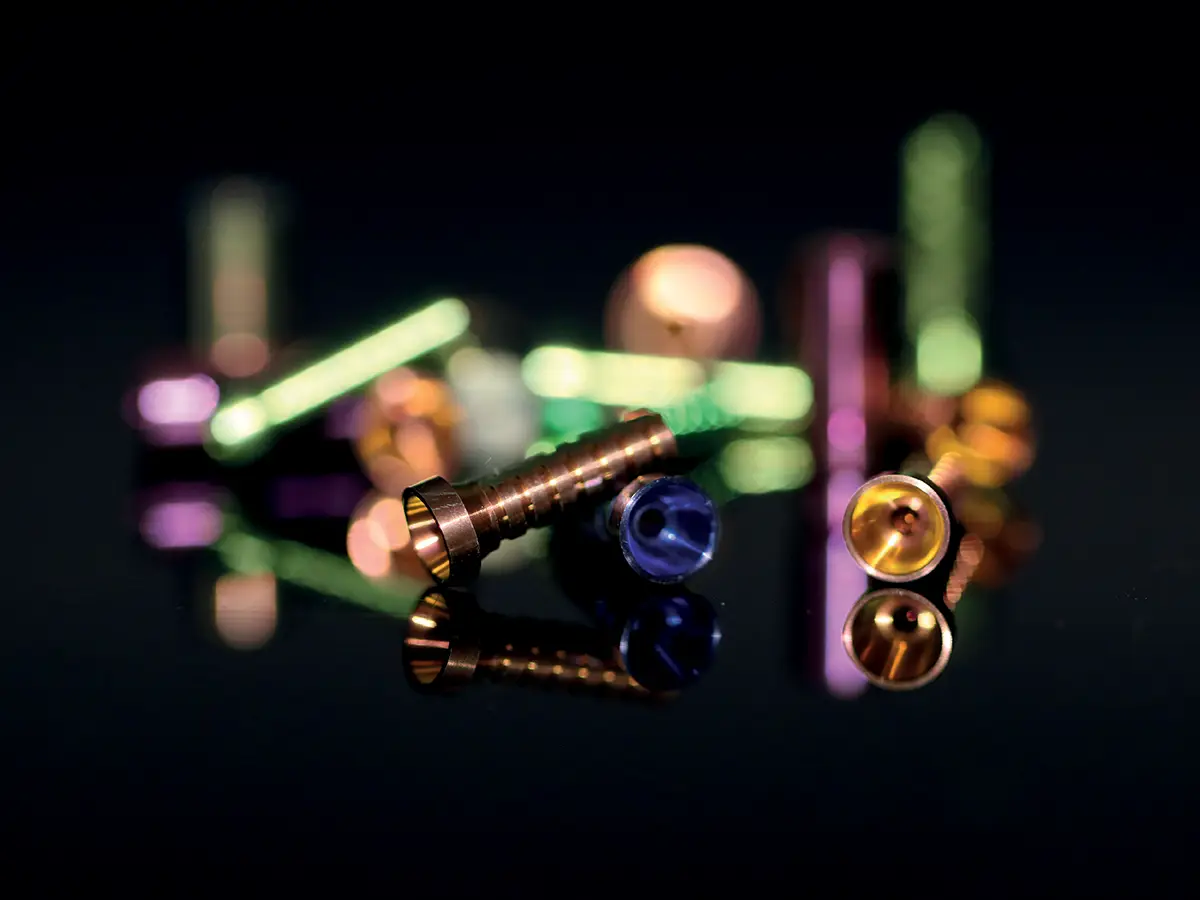
MILLED DETAILS PRODUCTION…
4. CAD/CAM Milling
For our clients, we design and mill details with up to 5-micron accuracy using the industrial, precision milling machines DMG MORI HSC 20 and DMG MORI HSC 20 ULTRASONIC. The production of milled details is applied in the medical industry.
5-axis milling machines provide speed and reliability of the process with acceleration > 2 g and spindle rotational speed during water cooling from 42,000 rpm to 60,000 rpm.
- Angular travel of axis C 0 degrees/360 degrees
- Angular motion axis – 10 degrees /130 degrees
- Magazine of 24 milling tools
PARAMETERS
- travel in the X-axis – 200 mm
- travel in the Y-axis – 220 mm
- travel in the Z-axis – 280 mm
- detail diameter – 200 mm
- height of the processed object – 200 mm
- detail weight – 100 kg
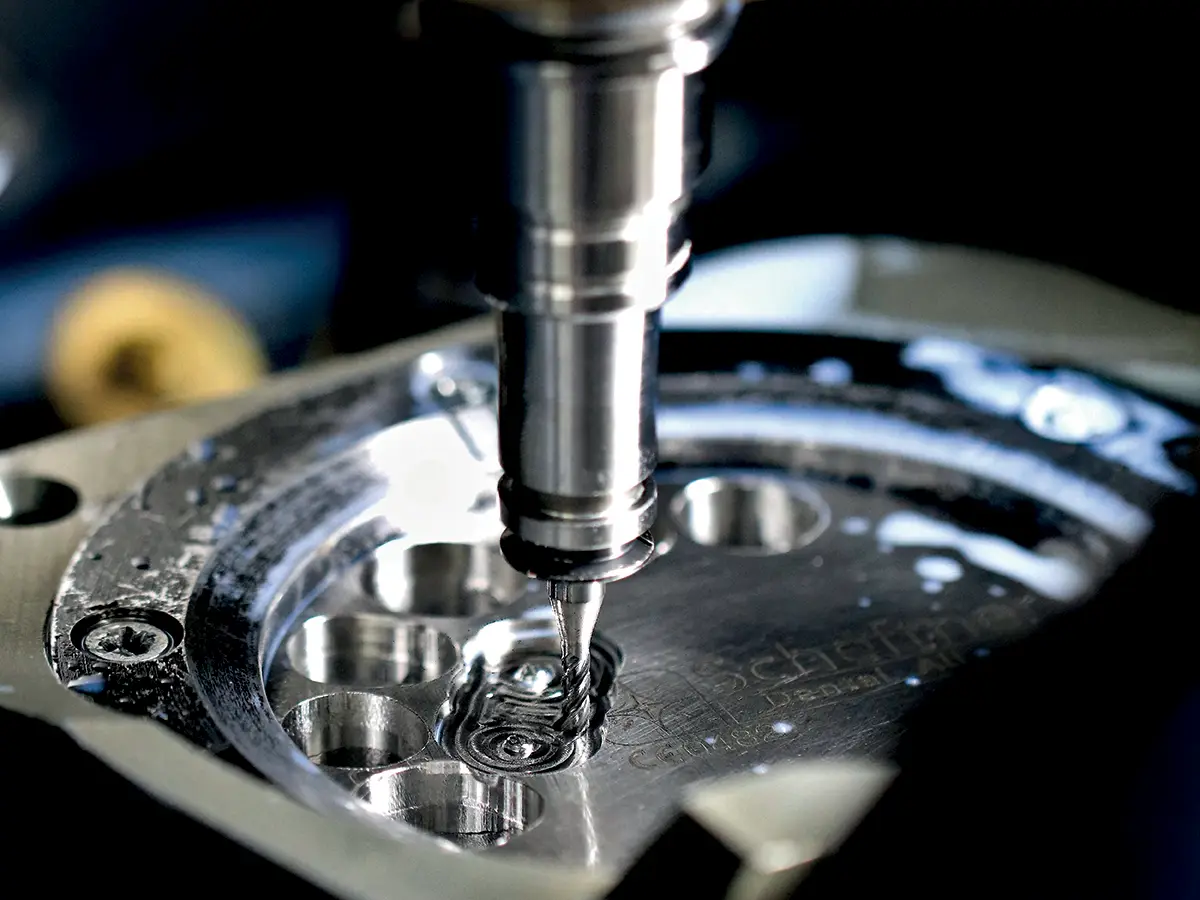
PRODUCTION OF PLASTIC ELEMENTS…
5. Injection Molding of Thermoplastics
Production of plastic elements from granulate into a mold where it solidifies into a so-called molded part. The production of various elements involves injecting plasticized plastic from granulate into a mold where it solidifies into a so-called molded part. A wide range of applications is allowed by the following materials:
- Plastics: black polypropylene PP, white and clear regranulated polypropylene, ABS polystyrene, LDP regranulated polyethylene.
- Engineering plastics: ABS, ABS/PC, ASA, PMMA, PC, PA, POM, PET, PBT, PP, PE, PS, PPO.
- High-temperature plastics: PEI, PPA, PPS, P.
- Thermoplastic elastomers: TPU, TPS, EVA..
POSSIBILITIES AND APPLICATION
The injection molding technique ensures uniform material preparation and precise injection, which is the basis for the high quality of the produced structures. Production using thermoplastic injection is applied in many industries, but the most common are: medical technology elements, packaging, safety products in the automotive industry, and precise details.
Electric drives provide high efficiency and repeatability, and innovative drive technology makes injection molding machines with clamping force ranging from 350 to 6500 kN reliable. Reproducibility and quality of parts thanks to a play-free, directly acting pulling screw. The use of a liquid-cooled servo-electric drive means that the injection molding machine has a low emission level.
After agreeing on the specifications of the injection mold and selecting the material, we determine the unit price of the detail.
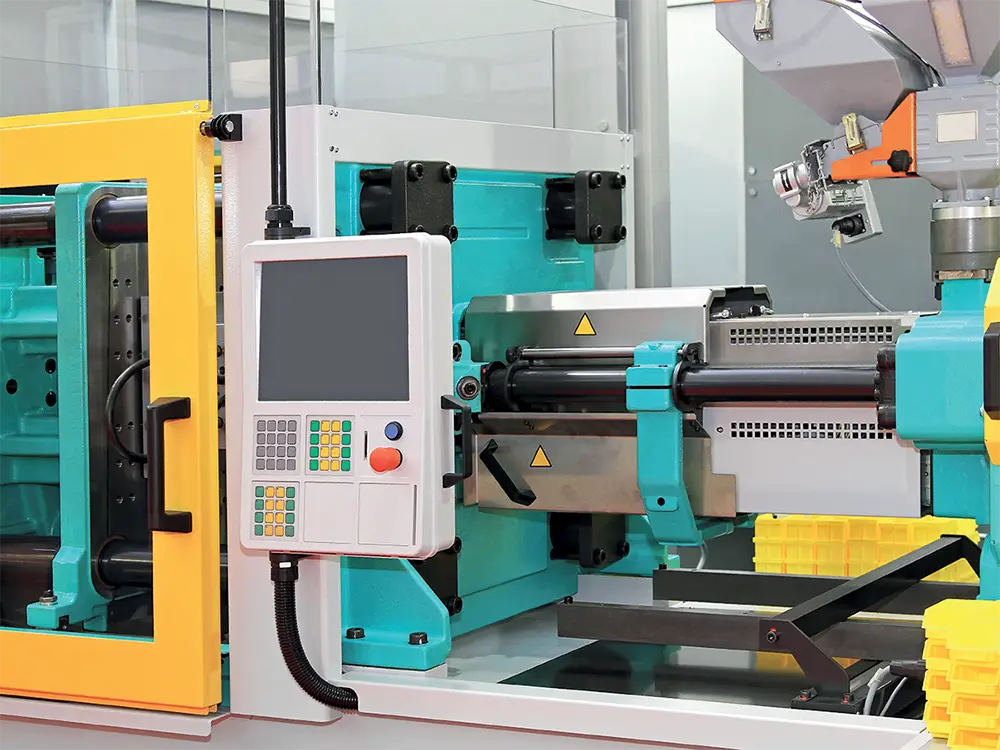
A qualified team oversees the entire production process and is always ready to answer your doubts or questions.
Webdesign – Piotr Sierant